摘要:针对将乐梅花隧道浅埋暗挖段V级围岩破碎、透水性强、自稳能力差的地质条件, 为提高围岩强度, 降低围岩透水性能, 增强隧道掘进时围岩的稳定性, 提出采取高压注浆地表加固技术措施, 进而改善隧道受力拱作用, 为隧道掘进提供安全保障。
关键词:隧道浅埋暗挖段; 地表加固; 技术分析;
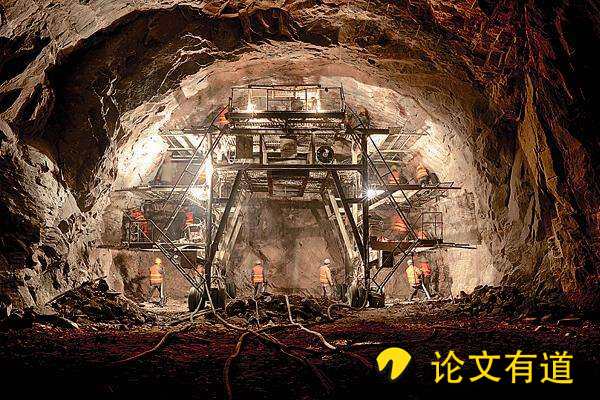
1 工程概况
将乐梅花隧道是省道S308 (纵七线) 将乐县梅花至玉华段公路的一部份,设计桩号为K1 240~K2 370,全长1130m,为长隧道。本隧道区内构造相对稳定,节理裂隙发育,岩石较破碎,且易形成排水通道,隧道洞身围岩受其影响,围岩级别降低。本隧道为单洞双车道,洞身净宽14m,设计速度40km/h,二级公路标准。
桩号K1 750~K1 800为隧道浅埋段,且在K1 780处存在F2断层破碎带,破碎带发育,沿断层带岩石硅化强烈,局部发育断层泥和劈理化带。断层角砾及擦痕、阶步等特征显示,本带是多期多阶段构造叠加、复合的产物,地质情况复杂,围岩差,在施工中易发生坍塌,极端情况会出现冒顶。K1 760~K1 785段为两山之间低洼平地,最小覆盖层厚度12.3m,最大覆盖层35m,两边山坡地势较陡峭。根据该段地勘资料ZK2显示,主要有粉质粘土堆积层,厚度在2.2~5.3m,破碎状的强风化粉砂岩,厚度在12.2~19.7m,在洞身局部有中风化粉砂岩。浅埋段区域地表水主要分布于山间沟谷中,隧址区内未见常年性溪流,仅沟谷当中在降雨后出现间歇性水流,流水主要接受大气降水的补给,受季节性影响变化较大。基岩构造裂隙水赋存于基岩的裂隙中,受构造发育情况控制,一般地区导水性弱,但构造破碎带附近,其导水性较好,主要接受大气降水及地下水侧向补给,水量变化较大,对隧道施工影响较大。
2 地表加固技术措施
针对浅埋段V级围岩地质条件差,在施工过程易发生坍塌、冒顶等地质灾害,为提高围岩的强度,降低围岩透水性能,增强隧道掘进时围岩的稳定性,在隧道洞身与地表间采用高压注浆地表加固技术措施,在隧道开挖轮廓线外6m范围内形成受力拱,如图1所示。钻孔注浆分三部分进行: (1) 在隧道初支外两侧打入Φ108钢管,90°垂直钻孔,长度约25m,间距1.5m×1.5m,梅花形布置,如图2所示。 (2) 在隧道范围内拱顶打入Φ76钢管,90°垂直钻孔,长度约15m,直至隧道开挖面,间距1.5m×1.5m,梅花形布置,如图3所示。 (3) 在两侧山脚之间打入Φ76钢管,6°至18°斜向钻孔,长度20~25m,间距1.5m×1.5m,梅花形布置,两侧各布置4排,如图4所示,第一排呈垂直打入,第二排注浆孔方向角度与第一排垂直夹角呈6°,第三排注浆孔方向角度与垂直夹角呈12°,第四排注浆孔方向角度与垂直夹角呈18°。加固方式采用水泥单液注浆,标号为M30,水泥采取42.5R级普通硅酸盐水泥,水灰比0.5∶1,注浆压力1~3.0MPa.注浆顺序为先注浆靠山一侧,再注另一侧,然后再注中间的,注浆顺序宜按单、双孔序孔进行,即先跳孔跳排,注单序孔,然后注剩下的双序孔。为确保浅埋段安全渡过,地表注浆加固在洞身开挖前7天完成。
图1 节理裂隙带断层注浆示意图
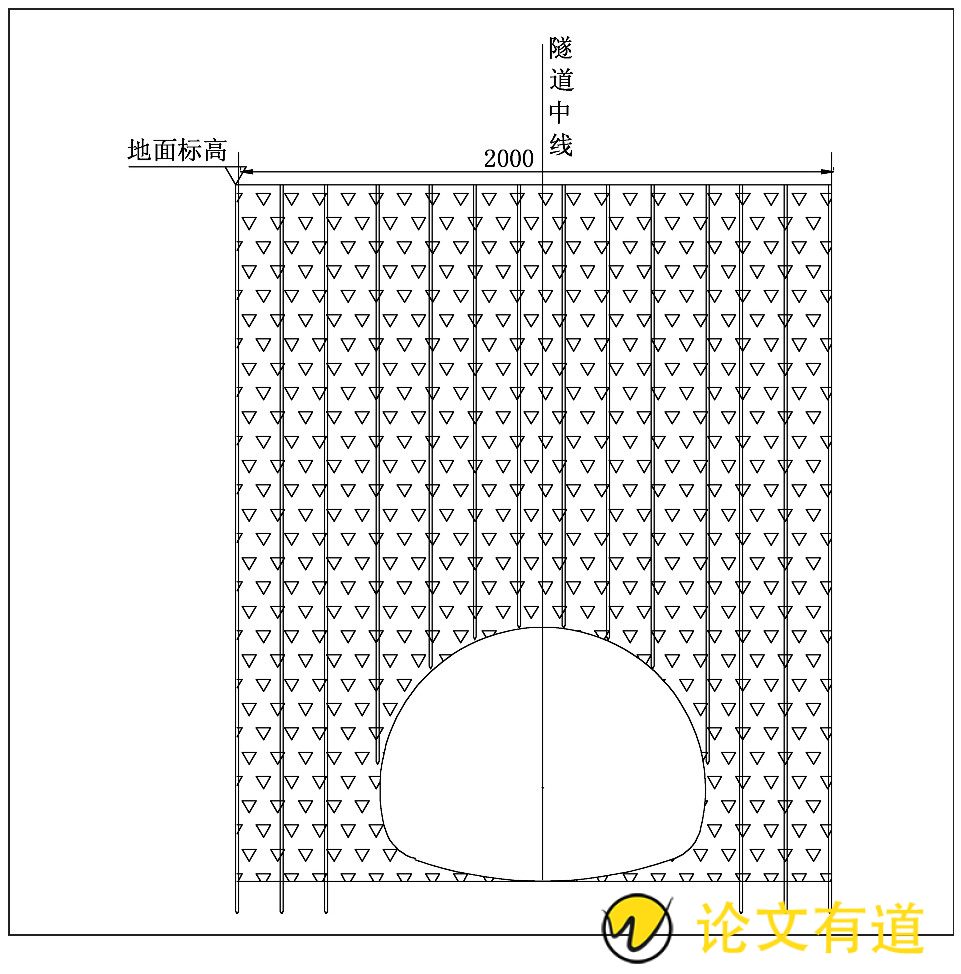
图2 隧道初支两侧加固示意图
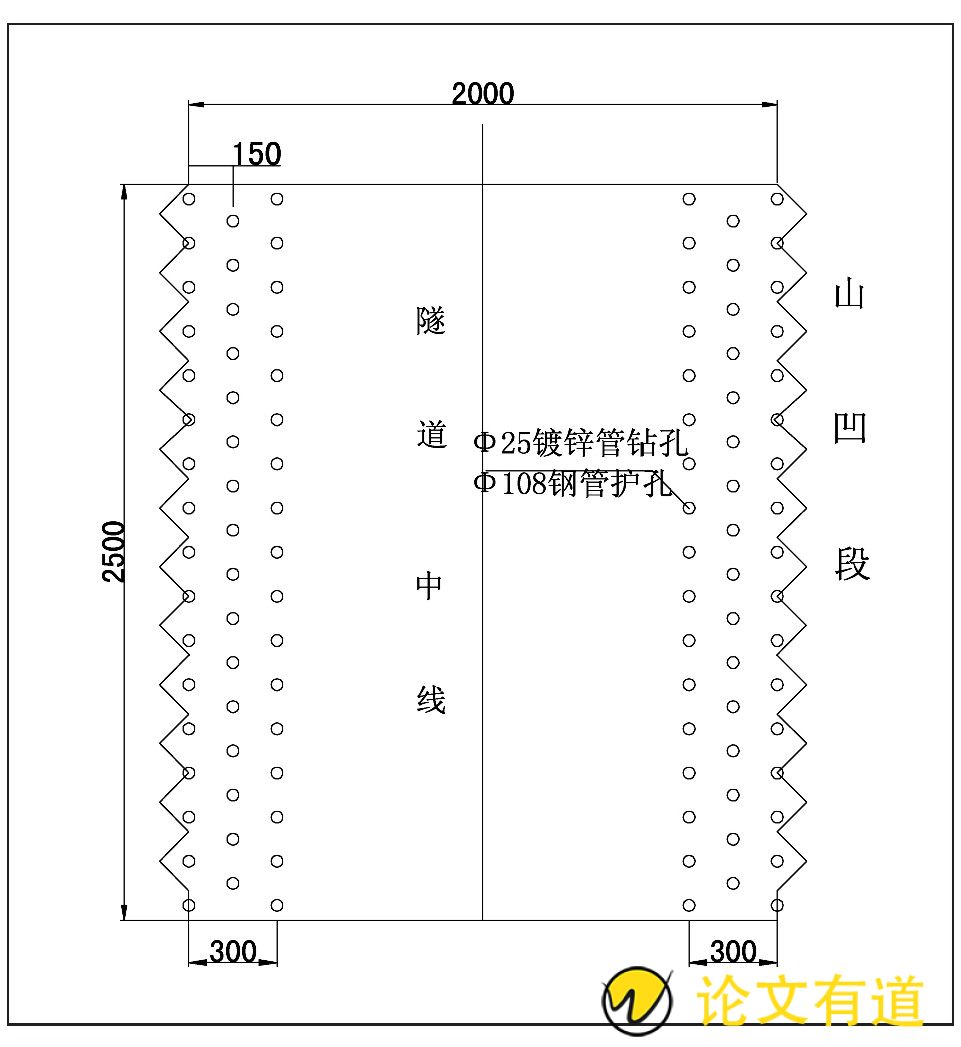
图3 隧道拱顶加固示意图

图4 隧道浅埋段纵断面图及山脚段加固改造图
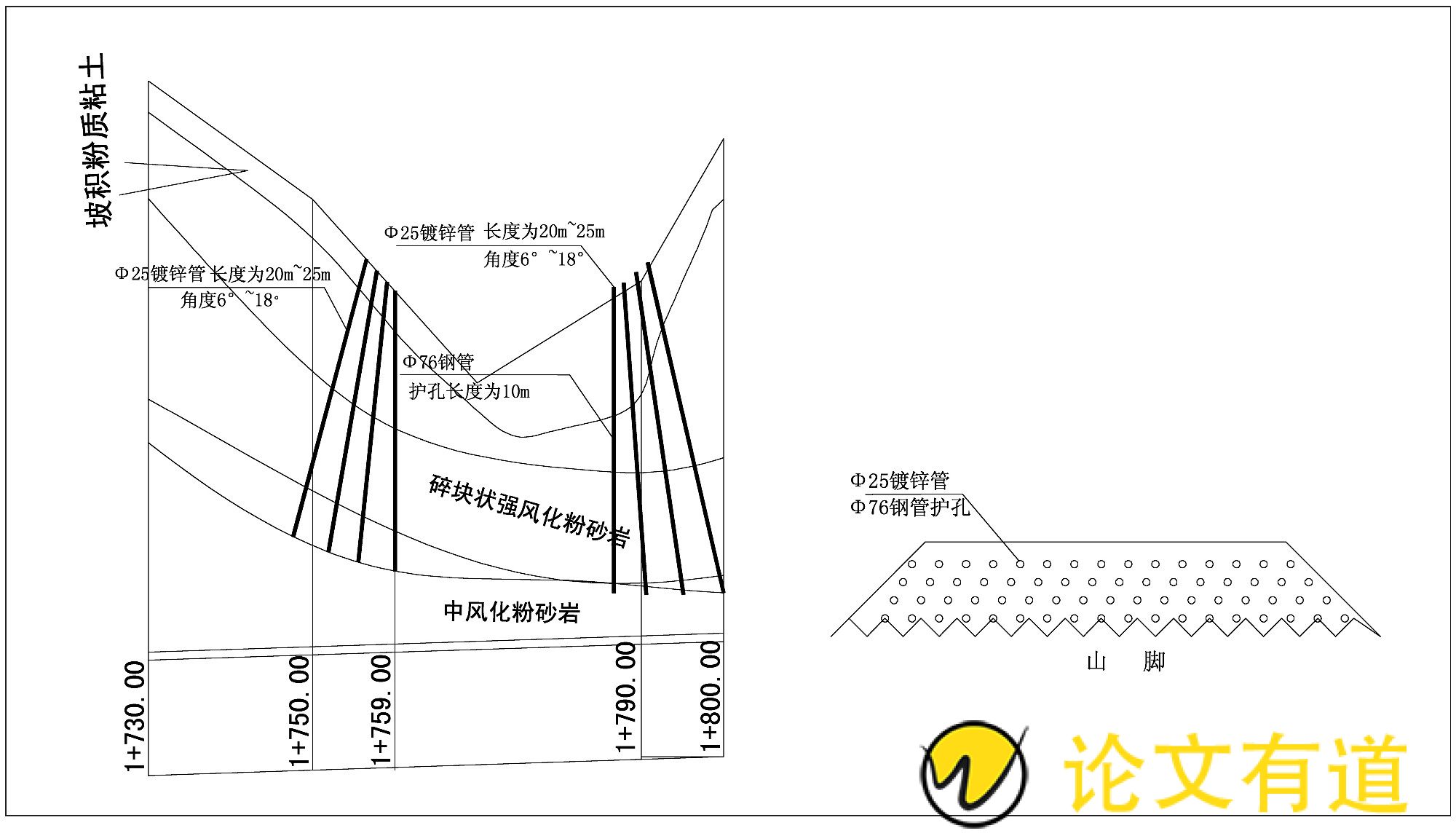
3 施工工艺
3.1 工艺流程
测量放样→钻孔布点→钻机就位钻孔→下管→注浆→二次 (劈裂) 注浆→结束。
3.2 施工技术
3.2.1施工准备
(1) 在开钻前对加固范围内场地按统一标高进行平整,地表采用厚15cm素混凝土喷层,避免地表水下渗软化围岩并起到稳压层的作用,根据地形水文情况,在施工区域上方15m处设置截水措施,在下游15m处挖坑降水。
(2) 按批复的施工方案组织人员、机械设备及材料等进场,按相关要求进行检测后及时按程序报批。检查搅拌机、注浆泵等设备运转情况并做好各易损件的筹备工作:用1.5~2倍于注浆终压对系统进行注水试验检查,并接好水、电;检查管路系统能否耐压,有无漏水,连接是否正确;检查设备机况是否正常;使设备充分热身,试运转时间为20min.
(3) 施工前,项目部严格按照设计要求及有关规范规定对施工班组进行技术交底,作好施工前安全文明教育,在施工人员掌握设计意图、技术要求、施工顺序后再进行注浆加固工程的施工。
3.2.2 试验孔施工
(1) 根据设计要求选定Φ108-2#孔、Φ108-100#孔和Φ76-188#孔作为试验孔,利用全站仪放样出孔位,钻机就位固牢后开钻。过程中需检查钻杆的垂直度不得大于1%,如有偏差则利用钻机进行修孔,保证成孔后的垂直度。在成孔后采用挖机进行下管,钢管则按设计要求提前进行加工,接口采用焊接,接口质量检查合格方能下管,在下管到位后施工长度不小于1m的止浆塞,在止浆塞砼达到一定强度后进行注浆施工。
(2) 注浆停止条件采用定量-定压相结合的方法控制,当注浆压力逐渐上升, 流量逐渐下降, 注浆压力达到设计终压并稳定10min后, 即可结束该孔注浆。当长时间注浆压力不上升或注浆压力在较小值附近, 且单孔注浆量达到设计单孔注浆量的2倍时, 可结束该孔注浆,施工情况如表1所示:
表1 试验孔钻孔注浆情况表 (施工时间:2018.12.9~12.10)
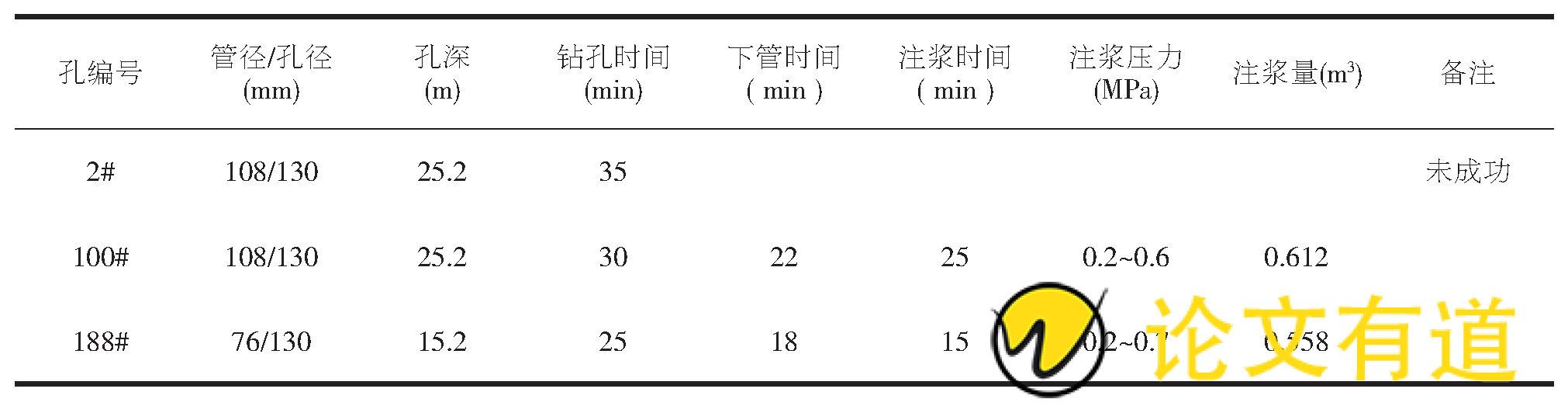
(3) 施工中存在的问题
(1) 在2#孔钻孔到位后,钻机移位及到下管时间间隔63min,在下管到18m深度时发现无法下管,原因为钻孔完成后停滞时间过长,孔内塌孔而无法下管到位。
(2) 在注浆过程加压时,钻孔的止浆段有上浮现象,致使注浆无法持续加压,在孔口先是地下水冒出,持续注浆后出现浓浆,止浆措施达不到止浆的作用。
(3) 在施工过程中发现浅埋段地下水位较高,成孔后观察地下水位在地面下5m左右,对注浆质量存在影响。
(4) 解决措施
(1) 单孔成孔时间控制在25~35min,注浆时间在15~25min,在成孔后应在30min内完成下管且时间不得超过30min.
(2) 完成下管就位后第一时间施工止浆塞,止浆塞的长度应不低于1m,经12个小时后再进行注浆作业,以免止浆措施达不到效果。
(3) Φ108-100#孔与Φ76-188#孔注浆压力达到0.6~0.7MPa,注浆量分别为0.612m3与0.558m3,钻孔内体积分别分0.202m3与0.131m3,则扩散的注浆量为0.208m3与0.227m3.在孔口出现浓浆时停止注浆作业,综合地下水位的影响,根据注浆量推算扩散半径达不到设计要求,注浆效果不理想。
(4) 针对试验孔注浆效果不太理想的情况,并综合考虑地下水对钻孔注浆的影响,结合以往类似的工程经验,对原设计的方案进行了优化:注浆工艺采用二次劈裂注浆进行施工,取消原设计的Φ76与Φ108钢花管段,保留实管段作为护壁,防止注浆孔在地质不良段发生坍塌,在孔中先预埋一根Φ25镀锌管,长度为高出孔深至少50cm,并在原设计的注浆段长度范围内对Φ25镀锌管进行钻孔,钻孔外圈需用塑料胶布绑扎两层,避免第一次注浆时水泥浆渗入。第一次注浆时注浆管需伸至孔底,在孔口冒出浓浆时再慢慢拨出。第一次注浆时孔内地下水排水需预先用人工挖出小排水沟进行外排,避免地下水乱排导致场地杂乱影响施工。注浆过程做好施工记录,待一次注浆完成12h后进行二次注浆,利用较大的注浆压力,将浆液注入地层中,浆液以填充、渗透和挤密等方式,赶走破碎土及岩体裂隙中的水分和空气,并占据其位置,形成“结石体”,使原来松散围岩胶结成一个整体,从而达到稳定围岩的效果,保证隧道施工的安全。注浆工艺如图5所示。
图5 注浆工艺示意图
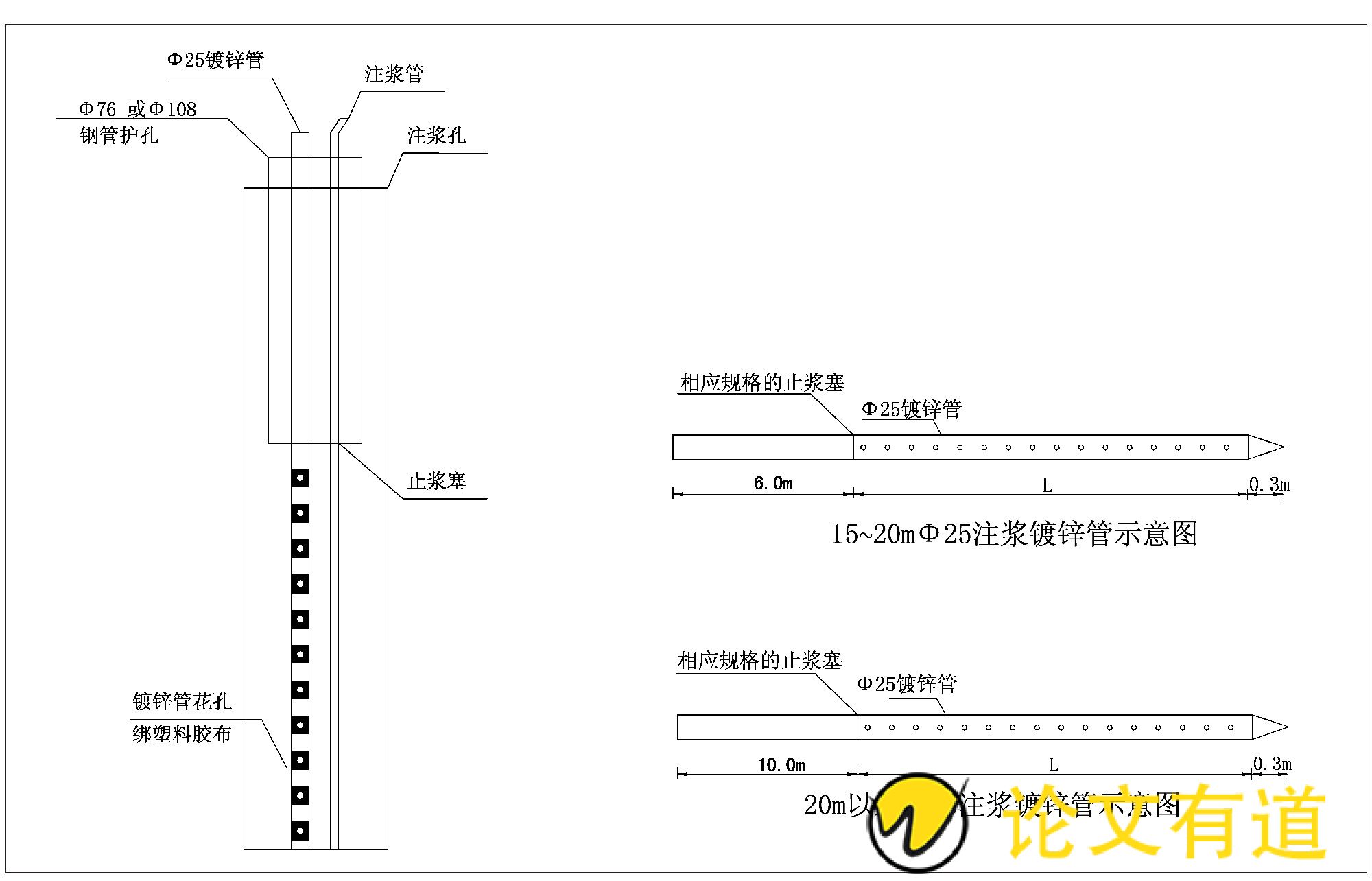
3.3.3 钻孔与注浆施工
(1) 桩位放样
根据设计图纸确定钻孔位置、钻孔深度,对桩位进行统一编号,在地面按编号用小木桩进行布孔。
(2) 钻机就位钻孔
(1) 对钻机进行调整复测桩位坐标,确保钻机准确定位及牢固,开钻后记录每节钻杆长度,确保钻孔深度。钻孔设备采用履带式钻机,配备3名机手,成孔后及时进行钢管接桩,避免出现塌孔返工现象。
(2) 钻孔位置依据平面图施放,孔位偏差不大于5cm,钻孔采取隔孔进行,成孔的深度比设计孔深超出50cm,避免在未下管或下管过程中钻孔坍塌达不到设计孔深。
(3) 下管与注浆
(1) 钻孔完成后按设计要求下一根Φ25塑料管,塑料管单根长度4m,根据孔深搭配塑料管,确保二次注浆塑料管伸入钻孔底部,再对塑料管6m长度进行钻孔,钻孔间隔25~35cm,用胶带缠绕两圈,二次注浆时当压力达到一定程度,能在钻孔位置爆开,水泥浆液在此位置扩散。塑料管底部、连接接头需密封好,防止第一次注浆时水泥浆液进入管中,完成后继续下注浆管。
(2) 制浆时通过制浆桶水的体积根据水灰比,确定每次制浆加入的水泥量,并采用比重计对所制浆液进行检查。制浆搅拌时间不少于5min,制备好的浆液不得离析、不得停置时间过长,制成浆液 (未加早强剂) 停留时间不超过4h, 水泥浆经过滤后进入储浆罐。
(3) 先利用注浆管对孔位进行洗孔,确保水泥浆液与孔壁有效粘结,待孔内泥浆清洗干净后进行第一次注浆 (注浆压力0~0.5MPa) ,待孔内水排出后注浆停止,凝固12~24h后进行第二次注浆,注浆利用之前预留Φ25塑料管进行,压力在1~8MPa.开始注浆时因管内处于密封状态,压力会很快到达4~8MPa,冲破塑料管钻孔位置胶带后压力值稳定并慢慢降至1.5~3.0MPa,待注浆量达到设计单孔注浆量2倍或地下水挤压出地面后注浆停止。
(4) 施工要点
(1) 钻孔时应保持孔的垂直度,倾斜度不得大于1%,因岩层破碎,在钻孔完成后应及时清孔下管,避免钻孔坍塌造成无法下管,并做好钻孔相关记录。隧道轮廓线范围内的钻孔孔深必须根据地面标高与隧道开挖轮廓线标高进行计算得出。
(2) 在注浆全部结束且达到一定强度时,可进行取芯判定验证注浆效果,当注浆不能达到效果时可进行补注浆或在洞身施工时根据注浆质量进行隧道动态设计,确定隧道施工安全与质量。
(3) 每5m设置一个沉降观测点,在隧道洞身施工前进行观测,随时掌握浅埋段沉降情况。
(4) 注浆时严格按已批复的配合比进行搅拌,保证拌浆的连续性,注浆从外围进行围、堵、截,内部进行填、压,以获得良好的注浆效果。
(5) K1 780断层破碎带宽度为2~4m,钻孔时应测量出断层带位置,在范围内适当加密孔数,并通过钻孔验证断层破碎带真实情况。
(6) 断层破碎带周围注浆时,应先进行断层破碎带范围外的钻孔注浆,再进行断层破碎带范围内的钻孔注浆。应掌握注浆实时情况,遇到注浆量大且压力一直无法上升时应停止注浆,在水泥浆初凝时间快到前再进行注浆或采取双液注浆,单液注浆量按其他区域钻孔或试验孔的注浆量2倍进行控制。在取芯验证时在断层破碎带范围内需至少取一个孔验证注浆质量,作为洞身施工时是否要加强施工措施的依据。
4 注浆效果分析
在钻孔注浆完成后,通过钻芯取样进行钻孔注浆质量检测,通过对取样岩芯进行结石率测试,了解浆液在地下的终凝程度,再对结石体进行抗压强度测试,检验其强度是否满足设计要求。试验结果表明:岩体结石率达到96.7%,符合规范岩体结石率必须达到95%以上的要求;岩体28d平均抗压强度达到9.5MPa,符合规范28d极限抗压强度不低于5.8MPa的要求。同时通过注浆取得如下效果:
(1) 施工安全得到保证。目前该隧道浅埋段已采用小导管超前支护及双侧壁导坑法顺利进洞并实现隧道贯通,开挖与初期支护已全部完成,施工中未出现坍塌或冒顶等安全事故,保证了隧道工程的施工安全。
(2) 工程质量得到保证。通过地表注浆加固,有效地隔绝了地表水,降低围岩的透水性能,大大改善了原有岩层的物理力学性能,提高了围岩的自稳时间和承载能力,减少了初期支护的围岩压力,保证了钢支撑锚喷等初期支护长期稳定,提高初支结构安全。施工中通过地表沉降、洞内收敛及拱顶下沉进行监控量测,最大地表下沉值19mm,最大拱顶下沉值23mm,最大水平周边收敛值12mm,量测结果满足设计规范要求,围岩和初支变形已稳定,施工中未发现初支开裂或渗漏水现象。
(3) 工期得到了保证。通过地表加固注浆处理,提高了围岩的自稳能力,加快了隧道的掘进速度,工作效率大大提高,缩短了浅埋段的施工工期。
5 结束语
梅花隧道浅埋暗挖段,对粉砂岩残积粘性土及碎块状强风化粉砂岩地表加固采用高压注浆地表加固方法有效可行,第一次注浆可确保水泥浆液与孔壁有效粘结,防止塌孔,第二次劈裂注浆,利用较高的注浆压力使水泥浆液有效扩散,满足设计要求的扩散半径,在隧道开挖轮廓线外加固形成受力拱,使得隧道开挖过程中洞内没有发生塌方,初期支护和二次衬砌也没有开裂,隧道的变形都在允许范围内,有效地保障隧道的施工安全。
参考文献
[1] 李明亮, 王国体, 刘志楠, 鲍大春。公路隧道浅埋段地表加固分析[J].工程与建设, 2011 (02) :248-249.
[2] 任永胜, 张志耕。隧道浅埋破碎带地表注浆预加固技术[J].内蒙古公路与运输, 2009 (04) :35-37.
[3] 安永林, 彭立敏, 张峰, 吴波。隧道施工时地表沉降监测控制标准探讨[J].岩土力学, 2009 (S2) :446-451.
[4] 马海君, 郝行舟。浅谈地表注浆加固在不良地质隧道中的应用[J].交通科技, 2005 (06) :67-69.